Column #10
December 9, 2016
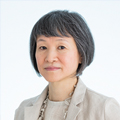
Cool Japan, a Life of Love for Fabrics
Textile DesignerReiko Sudo
I was born and raised in Kakioka in Ishioka city located two hours north of Tokyo by train and on the north side of Mount Tsukuba. It’s a rural town with abundant nature and known for having apples in the southern end and mandarins in the northern end. At the time of my birth in 1953, many women wore kimonos. Around this time, TV broadcasting began, the first Christian Dior fashion show took place in Japan, and fashion styles such as the A-line and Y-line became extremely popular. At the time, I was wearing children’s clothes hand-sewn by my mother from old adult kimono fabric. The clothes my mom made also emphasized the A-line, such as petticoats worn under skirts.
Anyway, Japanese kimonos when unstitched are composed of all the pieces of one original 13-meter fabric. The fabric of worn-out kimonos undergoes a process of being washed, stretched, and dried called “arai bari” in order to restore it as if brand new. In the olden days when there was good weather, one could observe a spectacle of kimonos hung to dry under Japanese roofs. It was done once every one or two years. The kimono would be unfastened, undergo arai bari, and be re-sewn. Each time they are washed with water, the resilience and luster of the fabric is restored. In those days the fabric of tsumugi, yukatas, and the like wasn’t double sided so they were restored many times and worn very carefully. Also, if there was a stain or dirt that wouldn’t disappear, dark colored ink would be carefully applied with a paintbrush in an effort to save the design alone. For the traditional art of dyed and woven goods, “gofun”, a kind of pigment made from ground shells is used, but discoloration can occur. At the time, yellowing could be corrected. Holes caused by tobacco burns, hook-shaped tears, and the like were also beautifully repaired through a mending process called “kaketsugi.” During the Meiji era, new re-dying techniques were developed. For example, kimonos were being re-dyed in dark hues. Specialty “Kuro Some” shops opened and offered services to re-dye fabric in a variety of colors and patterns.
ReMUJI by Muji
When fabric was considered precious in that way, we came up with a variety of new ideas in order to handle kimonos with great care. A project has started that is about learning from our ancestors’ careful fabric ingenuity and considering what we can do living in modern times. Ryohin Keikaku, which I give design advice to, is participating in the “FUKU FUKU Project”. The aim of this project is to collect unneeded clothes in an effort to recycle such resources and convert them into energy. Also, I am working on the “ReMUJI” project launched in 2014. ReMUJI clothing is made anew from collected clothes that have been carefully washed and re-dyed in a color that originated in Japan, “indigo blue”. During the Edo era, an original dying method was created, and “Japan’s indigo” was showered with praise from around the world. The project reminds us of the olden day “kouya” dyer shops that were everywhere in Japan, even in small towns.
Currently in the U.S., New York disposes of 200,000 tons of unneeded clothes and textiles, and the entire country disposes of 12.65 million tons per year. Against this backdrop, the long-running exhibit “Scraps: Fashion, Textiles & Creative Reuse” opened at the Cooper Hewitt Smithsonian Design Museum in New York on Sept. 23, 2016 and will run through April 16, 2017.
Scraps Exhibit in New York
Naturally, “scrap” items are the main feature, but the exhibit introduces projects that aren’t simply about recycling scraps. The projects also present new merits and design that looks ahead to a “new era” in recycling processes. The work of three designers is on display. Luisa Cevese, founder of Riedzioni in Milano, recycles discarded, torn up selvage from the manufacturing of textiles with rapier looms. Also, Christina Kim, founder of the LA fashion brand popular around the world, Dosa. Her project uses fabric left over from the manufacturing process of clothes made from India’s delicate handspun and hand loomed jamdani. And our company, NUNO, is exhibiting the “Kibiso Project,” which works together with the silk producers of Tsuruoka city, Yamagata. This project started in 2008 in an effort to recycle waste and by-products of silk spinning factories. When a silkworm makes its cocoon, the beginning of the thread they produce is called the “kibiso” and the end is the “ogaramichoshi”. Together with the Tsuruoka Silk Goods Industry Union in Tsuruoka City, Yamagata Prefecture, the project makes use of both parts which are usually thrown away. While visiting a silk spinning factory, I found tall stacks of “kibiso” and clusters of “ogaramichoshi” discarded in one of its corners. This is where the idea for the Kibiso Project came from. In the past, silk spinning factories recycled all the parts of the silk cocoon (i.e. byproducts), including the pupa which was eaten as a valuable protein source. People had the wisdom to not produce waste at all during this process.
The Scraps exhibit warns us about fashion that is worn just for enjoyment and sends a message about smart consumption. Since the era of kimonos, a variety of techniques that allow us to handle fabrics with care have emerged, and dwelling in the Japanese “mottainai” (waste not) spirit is the intention to maintain the value of objects and reduce wastefulness. I believe that the essence of “Cool Japan” is found in such ideas and practices.
PROFILE
Reiko Sudo
Textile Designer
After being a research assistant in textiles at the Musashino Art University Department of Industrial, Interior & Craft Design, Reiko helped found the company NUNO.
She is currently the managing design director of the company as well as a Tokyo Zokei University professor and is on the Muji design advisory board.
Some of the awards she has received include a Mainichi Design Award, Roscoe Award, and Japan Interior Designers Association Award.